24 hours. That's how long it now takes Enstone to digitalise, produce and wind tunnel test new development parts that come out of the drawing office. The technology behind this spectacular leap forward is stereolithography, an automatic, computer-assisted process for the manufacture of components in resin. The principle is simple: after the initial design of development components on a work station, half-scale models are produced for wind tunnel testing purposes using a machine provided by 3D Systems, known as Advanced Digital Manufacturing (ADM).
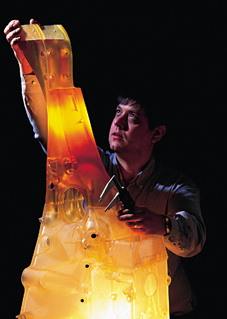 |
Pic. 1
|
ADM even enables complete assemblies such as suspensions to be produced, and not just isolated components. Last but not least, the R23 features some 20 components directly manufactured using ADM technology. The future of the system looks promising and Renault F1 team is already able to produce certain ceramic parts thanks to stereolitography and OptoForm, while the equipment to machine metal components will be available in the medium term.Engines also benefit. Our existing simulation tools give us a precise enough picture of the behaviour of a piston, a valve or a crankshaft, explains Race Team Manager Denis Chevrier. However, we use ADM to verify that the likes of pumps and other peripheral components are correctly integrated and also to optimise accessibility for the mechanics.
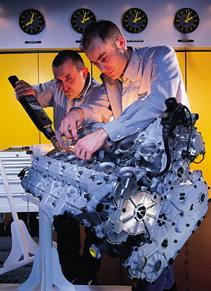 |
Pic. 2
|
Resin models: Controlled by computer to a precision of one tenth of a millimetre, a laser marks out the contours of the part to be produced by striking the surface of a tank of liquid resin which hardens upon contact with the beam. Millimetre by millimetre, the required part takes shape in a matter of hours.
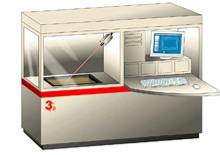 |
Pic. 3
|
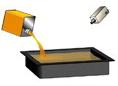 |
Pic. 4
|
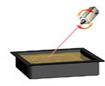 |
Pic. 5
|
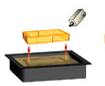 |
Pic. 6
|
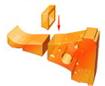 |
Pic. 7
|
|
|